آهن احیا مستقیم که به عنوان آهن آسفنجی نیز شناخته می شود از تبدیل مستقیم سنگ آهن به آهن توسط یک گاز کاهنده و یا کربن عنصری حاصل از گاز طبیعی و یا ذغال سنگ به دست می آید. در این روش انواع سنگ آهن تهیه شده از معادن را می توان مستقیما بدون تغییر و فرآوری خاصی استفاده نمود.
احیای مستقیم به فرآیند حالت جامد اشاره می کند که اکسید آهن را در دماهای پایین تر از نقطه ذوب به آهن فلزی احیا میکند. کلمه احیا یا همان کاهش در نام این فرآیند به دلیل استفاده از گاز های احیا کننده است که در کنار سنگ آهن در کوره ای با دمای 800 تا 1200 درجه سلسیوس به کار می رود. این گاز احیاکننده با نام گاز سنتز نیز شناخته می شود که معمولا ترکیبی از هیدروژن و کربن مونوکسید است.
شرح فرآیند تولید فولاد به روش احیا مستقیم
سنگ آهن ماده ای غنی از انواع اکسیدهای آهن (مگنتیت، هماتیت و …) است که برای تولید آهن باید اکسیژن موجود در سنگ آهن را از آن حذف نمود. بنابراین برای تبدیل سنگ آهن معدنی به آهن فلزی مورد استفاده در صنایع به انجام یک سری واکنش های شیمیایی در دمای بالا نیاز است. برای انجام این واکنش گاز احیایی معروف به “گاز سنتز” را در دمای بالا از اکسید آهن عبور می دهند تا اکسیژن موجود در اکسید آهن با گاز احیایی ترکیب شود؛ بنابراین اکسیژن از سنگ آهن حذف شده و با گاز عبوری ترکیب شده و از محفظه خارج می شود. در نتیجه مقدار زیادی آهن خالص و کمی هم ترکیبات آهن و کربن (به دلیل وجود ترکیبات کربنی در گاز احیایی) باقی می ماند. “واکنش های شیمیایی احیای آهن” مطابق فرمول های نوشته شده در زیر است:
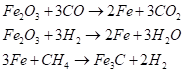
گاز خروجی این واکنش مجددا به محفظه سیستم ریفرمر باز می گردد تا با انجام واکنش شیمیایی ریفرمر دوباره بتواند به همان گاز احیایی اولیه تبدیل شود. واکنش های سیستم ریفرمر برای تولید گاز احیایی یا همان “گاز سنتز” مطابق معادلات زیر انجام می شود.
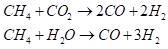
فرآیند احیای مستقیم به دو دسته پایه گازی و پایه ذغال سنگ تقسیم می شود. لازم به ذکر است که در این فرآیند عمل ذوب صورت نمی گیرد و دمای فرآیند پایین تر از دمای ذوب ماده اولیه است. در شکل زیر به برخی روش های رایج احیا مستقیم آهن اشاره شده است. روش pered نیز از این لحاظ که روشی ابداعی در ایران است در نمودار زیر آورده شده است.
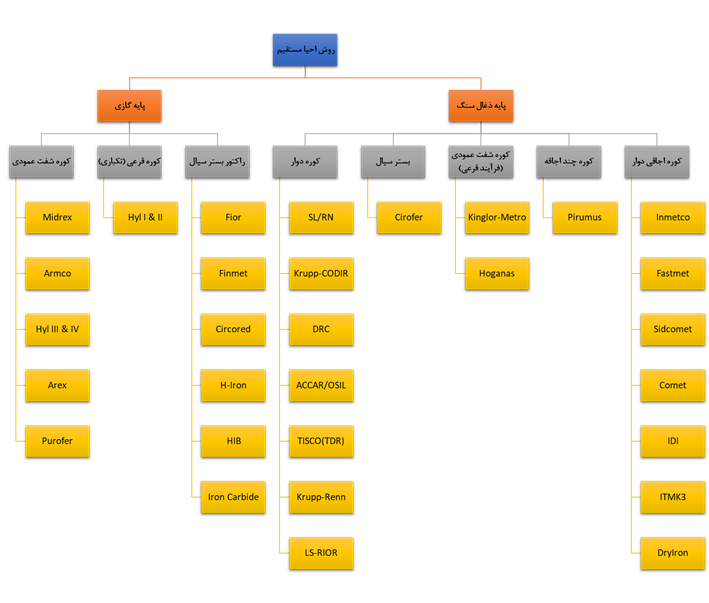
نمودار زیر گستردگی کاربرد و سهم هر کدام از روش های احیایی از تولید جهانی را ارائه می دهد:
روش های پایه گازی
روش میدرکس
با توجه به اینکه روش میدرکس یکی از پرکاربردترین روش های احیا مستقیم آهن است در ادامه دیاگرام شماتیک یکی از پتنت های این سیستم با نام HotLink ارائه می شود.
روش Pered
روش Pered نیز از آنجا که روشی اساسا ایرانی و شناخته شده جهانی است و در فولادسازی های: (شادگان، میانه، نیریز و بافت) مورد استفاده قرار می گیرد در ادامه توضیحاتی درمورد آن آورده می شود. این روش از زیرمجموعه های روش احیا مستقیم میدرکس است اما در شماتیک و کلیات روش تفاوت هایی نیز وجود دارد که این تفاوتها در جداول و شکل پایین ارائه می شود. لازم به ذکر است که محصول نهایی این فولاد سازی ها آهن احیا مستقیم سرد می باشد و طبق گزارش Midrex ظرفیت سالانه این فولاد سازی ها 0.8 میلیون تن در سال است.
جدول مقایسه میزان گاز طبیعی مصرفی در روش Pered و روش میدرکس
برای اطلاعات بیشتر و مقایسه کاملتر بین روش میدرکس و Pered به فایل جدول مقایسه رجوع شود.
فرآیند HYL
HYL یکی دیگر از فرآیند های احیا مستقیم پایه گازی و تا حدی مشابه فرآیند میدرکس است. در این روش ها از کوره هایی جهت حذف اکسیژن از کلوخه و گندله سنگ آهن استفاده می شود. فرآیند HYL در چندین نوع مختلف توسعه داده شده که همگی مکانیزم های تقریبا مشابه و یکسانی دارند و چهار روش HYL (I, II, III, IV) را شامل می شود. فرآیند HYL نیز در دو قسمت انجام می شود یکی از این مراحل تولید گاز احیایی و دیگری مرحله احیای سنگ آهن است. دمای روش فرآیند HYL در حدود 930 درجه و فشار فرآیند در حدود 5 اتمسفر است. گاز احیایی در قسمت ریفرمر از واکنش گاز طبیعی با بخار آب در حضور کاتالیست تولید می شود که این گاز شامل هیدروژن و کربن مونوکسید است که بخش زیادی از گاز تولید شده در ریفرمر را گاز هیدروژن تشکیل می دهد که قدرت احیایی بالایی دارد. اجزای اصلی جریان احیایی در مجاورت راکتور شامل: گرمکن افزایش دهنده دمای گاز احیایی تا دمای 925 درجه سانتیگراد، تجهیزات غبارگیر، خنکساز و حذف کننده آب از گازها، کمپرسور گاز بازیافتی و حذف کننده گاز کربن دی اکسید می شود.
مزایای HYL
با توجه به اینکه فرآیندهای HYL قبل از مرحله ریفرمر بخار شامل مرحله حذف گوگرد نیز می شوند می توان از مواد معدنی و گازهای دارای مقادیر بیشتر گوگرد نیز استفاده نمود. کنترل بهتری بر نسبت میان گاز هیدروژن و کربن مونوکسید به دلیل تجهیزات حذف انتخابی CO2 در سیستم گاز صورت می گیرد. این تجهیزات استفاده از رنج گسترده ای از نسبت بین گاز هیدروژن و کربن مونوکسید بسته به درجه متالیزاسیون و یا محتوای کربن مورد نیاز را امکان پذیر می سازد.
روش purofer
روش پروفر نیز مانند بسیاری از روش های دیگر از جمله مواردی است که پس از مدت کوتاهی کنار گذاشته شد. این روش از جمله روش هایی است که در مسیر پیشرفت فرآیند های احیا مستقیم راه اندازی شده و پیشرفت های بعدی آن در نهایت بهراه اندازی فرآیندمیدرکس منجر شد. زمان طولانی و دشواری از اولین ایده تا توسعه روش ها و فناوری های صنعتی می گذرد. کار اساسی در استفاده از چگالی گرم برای آهن احیا شده مستقیم ابتدا در آزمایشگاه انجام شد. سپس در اواخر دهه 1960 و اوایل دهه 1970 اولین کارخانه های آزمایشی ساخته و مورد بهره برداری قرار گرفتند. به عنوان مثال، فناوری ESSO-FIOR در کارخانه ای که توسط McKee در نوا اسکوشیا، کانادا ساخته و اداره می شد، آزمایش شد و فرآیند PUROFER Thyssen در یک مرکز نیمه صنعتی در Oberhausen، آلمان مورد ارزیابی قرار گرفت. با شروع در اواخر دهه 1970، اولین دوره های تولید پایدار کارخانه های احیای مستقیم با بریکت گرم با استفاده از فرآیند FIOR در ونزوئلا و کارخانه PUROFER در ایران انجام شد. پیشرفت نهایی این فناوری در اواسط دهه 1980 پس از بهره برداری موفقیت آمیز از اولین کارخانه MIDREX با بریکت گرم در صنایع گاز صباح (امستیل امروزی) در جزیره لابوان در مالزی رخ داد.
فرایند SL/RN
در فرآیند استاندارد SL/RNمواد اولیه: 1) سنگ آهن، 2) زغال سنگ، 3) دولومیت و یا سنگ آهک (به عنوان عامل گوگردزدایی) در یک کوره دوار شارژ می شود و توسط جریان گاز مخالف حرارت دهی صورت می گیرد. گرما از احتراق کنترل شده مواد فرار زغال سنگ و CO تولیدی مواد شارژ ایجاد می شود. احیای اکسیدهای آهن در حالت جامد در دمای بین 920 درجه سانتی گراد تا 1100 درجه سانتی گراد صورت می گیرد.
با هدف استفاده از سنگ معدن با عیار پایین تر، با توجه به مسائل دسترسی به کلوخه سنگ آهن و مقدار روزافزون سنگ معدن و کنسانتره در روش های نوین SL/RN این فرآیند تا حدی توسعه داده شده است که این روش ها این امکان را می دهد تا تنها در یک کارخانه مستقیما کنستانتره را به آهن احیا مستقیم تبدیل نمود که در واقع فرآیند های گندله سازی و احیا مستقیم در یک فرآیند ادغام می شود.
واکنشهای احیا و تولید گاز زغالسنگ به طور همزمان در داخل شارژ انجام میشود. DRI تولید شده و کسر غیر مغناطیسی باقیمانده پس از خنک شدن به صورت مغناطیسی از هم جدا می شوند. گاز زائد از یک بویلر عبور می کند تا گرما برای بخار و تولید برق بعدی بازیابی شود.
ریزدانههای سنگ آهن حاصل از فرآیند تغلیظ غالباً در کیفیت های بالا (آهن زیاد و محتوای ناخالصی کم) تشکیل می شوند و بنابراین برای تولید DRI با کیفیت بالا بسیار مناسب هستند. متالیزاسیون محصول نهایی این روش احیا مستقیم 93% و کربن موجود در حدود 0.1 تا 0.2درصد است.
تجهیزات روش SL/RN شامل موارد زیر می شود:
- تجهیزات حمل و نقل مواد خام
- کوره دوار
- خنک کننده دوار
- محفظه پس از گداختن (ABC)
- بویلر حرارت زائد
- رسوب دهنده الکترواستاتیک
- امکانات جداسازی و جابجایی محصول
- در موارد پیشرفته این روش برخی تاسیسات گندله سازی نیز با روش ادغام می شود.
مزایا روش SL-RN
- 4این فرآیند با رنج گسترده ای از انواع مواد آهن دار از جمله: گندله، کلوخه معدنی، ماسه ساحلی، ایلیمینیت و همچنین ریزدانه های سنگ آهن قابیلت کاربرد دارد.
- این فرآیند همچنان یکی یکی از فرآیندهای پرکاربرد پایه ذغالسنگ برای احیای مستقیم کلوخه معدنی و گندله است.
- این روش می تواند با طیف گسترده ای از مواد احیا کننده همچون: ذغال سنگ زیر قیری و ذغال سنگ، ذغال سنگ قیری، و در موارد خاص نیز آنتراسیت و ذغال کک کار کند.
- با حرارت بازیابی شده در احیا مستقیم به روش SL RN می توان برق تولید نمود که این برق تولیدی قابلیت فروش دارد و همچنین می تواند برق مورد نیاز کارخانه را تامین کند؛ به همین دلیل الزامی به وجود برق برای راه اندازی کارخانه هایی که با روش SL RN کار می کنند وجود ندارد؛ علاوه بر این فروش برق تولیدی نیز موجب بازگشت بخش قابل توجهی از سرمایه راه اندازی می شود.
مقایسه روش احیا مستقیم و کوره بلند
در مقایسه با سایر فرآیند ها روش احیا مستقیم روشی مقرون به صرفه از لحاظ مصرف انرژی است. تولید فولاد به روش احیا مستقیم به سوخت کمتری نیازی دارد و این از لحاظ کاهش مصرف سوخت جایگزینی مناسب برای “کوره بلند” است. با توجه به ترجیح ورود مواد اولیه کوره قوس به صورت پیشگرم شده در دمای بالا معمولا محصولات احیا مستقیم با دمای بالا وارد کوره قوس می شود تا مرحله پیشگرم حذف شده و تا حد زیادی در مصرف انرژی صرفه جویی شود.
مزایای روش احیا مستقیم
فرآیند احیا مستقیم با هدف حذف دشواری های تولید در روش کوره بلند توسعه یافت. بر خلاف روش کوره بلند الزامی به اینکه کارخانه احیا مستقیم بخشی از یک کارخانه فولاد یکپارچه باشد وجود ندارد. بنابراین روش احیا مستقیم نسبت به یک کارخانه فولادی یکپارچه هزینه سرمایه گذاری کمتری را مطلبد. این روش برای کشورهای در حال توسعه که منابع ذغال سنگ آن محدود است اما قراضه های فولادی زیادی در دسترس است بسیار مناسب است. با توجه به همین شرایط هند بزرگترین تولید کننده آهن با روش احیا مستقیم است. این روش خود دسته بندی های مختلفی را شامل می شود که در ایران نیز روش های ابداعی از این روش وجود دارد.
عواملی که موجب اقتصادی بودن احیا مستقیم می شود
- آهن احیا شده تقریباً همان ترکیب آهن حاصل از کوره بلند را دارد، معمولاً 90 تا 94٪ محتوی آهن (بسته به کیفیت سنگ آهن اولیه)، بنابراین یک ماده اولیه عالی برای کوره های الکتریکی در کارخانه های کوچک است که به آنها امکان استفاده باقیمانده شارژ از ضایعات با گرید پایین تر و در عین حال تولید فولاد گرید بالا را می دهد.
- محصول آهن خروجی از کوره احیا مستقیم به دو شکل ممکن است مورد فرآیند قرار گیرد:
- ممکن است خروجی کوره به صورت داغ به کوره قوس الکتریکی منتقل شود که در این صورت از مزایای مصرف انرژی کمتر بهره وری می شود.
- ممکن است محصول خروجی کوره احیا مستقیم به شکل بریکت فشرده و تبدیل شود تا بتوان آن را به آسانی به محل مصرف مورد نظر حمل نمود (شکل زیر).
- فرآیند احیا مستقیم از سنگ آهن گندله شده و یا کلوخه به صورت مستقیم به عنوان ماده اولیه استفاده می کند که این مورد نوعی مزیت است. البته در روش های خاصی از این فرآیند همچون روش بستر سیال لازم است تا سایزبندی ذرات سنگ آهن صورت گیرد.
- در روش احیا مستقیم می توان از گاز طبیعی برای فرآیند احیا استفاده نمود که البته با توجه به فراوانی گاز در ایران این روش برای کشور ما بسیار به صرفه محسوب می شود.
مسائل و مشکلات روش احیا مستقیم
آهن تولید شده از فرآیند احیا مستقیم (آهن اسفنجی) به شدت در معرض اکسیداسیون قرار دارد و از همین جهت معمولا سریعا تحت فرآیند فولادسازی قرار می گیرد. لازم به ذکر است که محصول تولیدی تا حدی اشتعال زا نیز محسوب می شود و لازم است از این لحاظ مراقبت های لازم صورت گیرد. برخلاف کوره بلند که خروجی آهن نسبتا خام و خالص می دهد؛ آهن تولید شده در احیای مستقیم در صورتی که از “شارژ ورودی قراضه” استفاده شود تا حدی محتوی سیلیکا دارد که باید از فولاد حذف شود.
در زمینه تجهیزات احیا مستقیم آهن، مشاوره و راه اندازی انواع خطوط تولید فولاد می توانید با کارشناسان ویستا آسمان تماس بگیرید.
دسته بندی روش های احیا مستقیم بر اساس نوع کوره مورد استفاده
روش های احیا مستقیم آهن بر اساس نوع کوره مورد استفاده نیز دسته بندی می شوند از همین جهت انواع کوره های احیای مستقیم، مواد اولیه مصرفی و نحوه کاری فرآیندها در تصاویر زیر ارائه می شود.