فولاد گالوانیزه مهمترین محصول فرآیند گالوانیزه کردن است. گالوانیزه کردن به معنای استفاده از فلز روی (Zn) بر روی فولاد برای محافظت در برابر خوردگی است. انواع روشهای تجاری موجود برای اعمال پوشش فلز روی (Zn) و تولید فولاد گالوانیزه عبارتند از: گالوانیزهی گرم، گالوانیزهی مداوم، الکتروگالوانیزه، آبکاری روی (Zinc plating)، آبکاری مکانیکی، پاشش روی (Zinc spraying) و رنگآمیزی روی. هر یک از این روشهای گالوانیزه یا گالوانیزاسیون فولاد جهت تولید فولاد گالوانیزه، ویژگی های منحصر به فردی دارند. این ویژگی ها نه تنها بر قابلیت انجام فرآیند، بلکه بر فاکتورهای اقتصادی و طول عمر مورد انتظار پوشش نیز تأثیر میگذارند. روش اعمال پوشش، چسبندگی به فلز پایه، محافظت در گوشهها، لبهها و رزوهها، سختی، تراکم پوشش و ضخامت میتواند در بین روشهای مختلف تولید فولاد گالوانیزه بسیار متفاوت باشد.
تاریخچهی ثبت شده جهت تولید فولاد گالوانیزه به سال 1742 میلادی باز میگردد، زمانی که پی جی مالوین، شیمیدان فرانسوی، روشی را برای پوشش دادن فولاد با فرو بردن آن در فلز روی مذاب در ارائه ای به آکادمی سلطنتی فرانسه توصیف کرد. سی سال بعد، لوئیجی گالوانی (Luigi Galvani)، همنام با فرآیند گالوانیزه، اطلاعات بیشتری در مورد فرآیند الکتروشیمیایی که بین فلزات انجام میشود کشف کرد. تحقیقات لوئیجی گالوانی در سال 1829 زمانی که مایکل فارادی فرآیند فداشوندگی فلز روی را کشف کرد، بیشتر شد و در سال 1836، یک مهندس فرانسوی به نام سورل یک حق اختراع برای فرآیند اولیهی جهت تولید فولاد گالوانیزه به دست آورد. تا سال 1850، صنعت تولید فولاد گالوانیزه در بریتانیا سالانه از 10 هزار تن فلز روی برای محافظت از فولاد استفاده میکرد و در سال 1870، اولین کارخانه تولید فولاد گالوانیزه در ایالات متحده شروع به کار کرد. امروزه، گالوانیزه کردن یا گالوانیزاسیون تقریباً در همهی صنایع اصلی که در آن از فولاد استفاده میشود، یافت میشود. فولاد گالوانیزهی گرم دارای سابقه موفقیت آمیز و رو به رشدی در کاربردهای بیشماری در سراسر جهان است.
گالوانیزهی گرم یکی از پرکاربردترین ابزارهای محافظت از فولاد است. در این فرآیند، اعمال پوشش با استفاده از فرآیند غوطه ور شدن گرم انجام میشود. در این روش یک پوشش فلز روی (Zn) بر روی محصولات فولادی با غوطه ور کردن محصولات در حمام روی مذاب به دست میآید. فلز روی را می توان به عنوان پوشش بر روی فولاد در فرآیند غوطه وری گرم اعمال کرد زیرا نقطه ذوب پایینی دارد. از آنجایی که محصولات فولادی در فلز روی مذاب غوطه ور میشوند، فلز روی به داخل فرورفتگی ها و سایر مناطقی که دسترسی به آن دشوار است جریان مییابد و برای محافظت در برابر خوردگی، تمام نواحی با اشکال پیچیده را به طور کامل پوشش میدهد. قبل از اعمال پوشش، فولاد تمیز میشود تا تمام روغنها، گریسها، خاکها، پوستههای اکسیدی و زنگزدگیها از بین بروند. پوشش گالوانیزهی گرم بر روی بسیاری از مواد در اندازههای مختلف از قطعات کوچک مانند مهرهها، پیچها و میخها گرفته تا ورقها، لولهها و اشکال بسیار بزرگ استفاده میشوند. اندازه حمامهای روی موجود و جابجایی قطعات، اندازه قطعاتی را که می توان گالوانیزه کرد را مشخص میکنند.
از آنجایی که فرآیند گالوانیزه شامل غوطهوری کامل مواد در محلولهای تمیزکننده و روی مذاب میشود، کل سطوح داخلی و خارجی پوشش داده میشود که شامل داخل حفرات و تو رفتگیها میشود. اعمال پوشش کامل از اهمیت بالایی برخوردار است زیرا خوردگی در داخل برخی از سازه های توخالی که در آن محلها محیط میتواند بسیار مرطوب باشد، با سرعت بیشتری رخ میدهد. همچنین بستها و اتصلاتی که هیچ محافظی بر روی رزوهها ندارند، مستعد خوردگی هستند و بستها و اتصالات خورده شده میتوانند منجر به نگرانی در مورد یکپارچگی اتصالات ساختاری شوند.
فرآیند گالوانیزه به طور طبیعی پوششهایی را در گوشهها و لبهها با ضخامت حداقل برابر با ضخامت پوشش در بقیه قسمتها اعمال میکند. این به این دلیل است که واکنش بین آهن و فلز روی یک واکنش نفوذی است و بنابراین ساختار کریستالی پوشش، عمود بر سطح فولاد تشکیل میشود. از آنجایی که آسیبدیدگی پوشش به احتمال زیاد در لبهها رخ میدهد، بنابراین این محلها جایی است که به حفاظت بیشتری نیاز دارد. به طور کلی پوششهای اسپریشده تمایل طبیعی به نازک شدن در گوشهها و لبهها دارند.
پوشش روی و فرآیند خوردگی
خوردگی را میتوان به طور ساده به عنوان تمایل فولاد، پس از تولید و شکل دادن، برای بازگشت به حالت انرژی پایینتر و طبیعیتر خود در سنگ معدن در نظر گرفت. این گرایش به “قانون آنتروپی” معروف است. روشهای محافظت از فولاد در برابر خوردگی که استفاده میشوند عبارتند از (1) تغییر پتانسیل شیمیایی فلز با آلیاژسازی، (2) تغییر شرایط محیطی با کاهش عوامل خورنده و یا با استفاده از بازدارندهها، (3) کنترل پتانسیل الکتروشیمیایی با اعمال جریانهای کاتدی یا آندی و اعمال مواد آلی و پوشش های فلزی.
فلز روی دارای تعدادی ویژگی است که آن را به یک پوشش محافظ در برابر خوردگی بسیار مناسب برای محصولات فولادی در بیشتر محیطها تبدیل میکند. فلز روی علاوه بر ایجاد مانع بین فولاد و محیط اطراف، قابلیت محافظت کاتدی از فلز پایه را نیز دارد. فلز روی، که نسبت به آهن و فولاد آندی است، در هنگام آسیب دیدن پوشش، خورده شده و آهن یا فولاد را در برابر خوردگی و زنگ زدگی محافظت میکند. اگر پوشش گالوانیزه از نظر فیزیکی آسیب ببیند، همچنان به محافظت کاتدی از فولاد ادامه میدهد. اگر نواحی جداگانه فولاد زیرلایه توسط لکهای به قطر 6 میلیمتر در معرض دید قرار گیرند، فلز روی اطراف این نواحی را تا زمانی که پوشش دوام میآورد، محافظت کاتدیکی انجام میدهد (شکل 1).
عملکرد میدانی فوقالعادهی پوششهای روی ناشی از توانایی آن در تشکیل لایههای محصول خوردگی متراکم و چسبنده و نرخ خوردگی بسیار پایینتر از آهن و فولاد است (بسته به محیط، حدود 10 برابر تا 100 برابر کندتر). در حالی که سطح فلز روی تازه زمانی که در معرض اتمسفر قرار میگیرد بسیار واکنشپذیر است، یک لایه نازک از محصولات خوردگی (اکسید) به سرعت ایجاد میشود که سرعت خوردگی بیشتر را تا حد زیادی کاهش میدهد.
گالوانیزهی گرم محافظت در برابر خوردگی فولاد را به ویژه در محیط های سخت فراهم میکند. گالوانیزه گرم سه سطح مقاومت در برابر خوردگی را برای فولاد فراهم می کند که عبارتند از (1) حفاظت مانعی (barrier protection)، (ب) حفاظت کاتدی (cathodic protection) و (3) زنگار روی (zinc patina).
حفاظت مانعی اولین خط دفاع در برابر خوردگی است. پوشش گالوانیزهی گرم با جداسازی فولاد از الکترولیتهای موجود در محیط، محافظت را ایجاد میکند. تا زمانی که مانع سالم باشد، فولاد محافظت میشود و خوردگی رخ نمیدهد. با این حال، اگر مانع شکسته شود، خوردگی شروع میشود. از آنجایی که یک مانع برای ایجاد مقاومت در برابر خوردگی باید دست نخورده باقی بماند، دو ویژگی مهم حفاظت مانعی عبارتند از (1) چسبندگی به فلز پایه و (2) مقاومت در برابر سایش. ماهیت محکم، چسبنده و غیرقابل نفوذ فلز روی آن را به یک پوشش مانع بسیار خوب تبدیل میکند. پوششهایی مانند رنگ که معمولاً دارای سوراخهایی هستند، همواره در معرض نفوذ عناصری هستند که باعث گسترش سریع خوردگی در زیر لایه میشوند.
علاوه بر محافظت مانعی، گالوانیزهی گرم از فولاد به صورت کاتدی نیز محافظت میکند، به این معنی که فلز روی به طور ترجیحی و برای محافظت از فولاد پایه، خورده میشود. سری فلزات گالوانیک (جدول 1) فهرستی از فلزات است که به ترتیب فعالیت الکتروشیمیایی در آب دریا (الکترولیت) مرتب شده اند. این آرایش فلزات تعیین میکند که وقتی دو عدد از این فلزات در یک سلول گالوانیکی یا الکترولیتی قرار میگیرند، کدام یک از فلزات آند و کدام یک کاتد خواهد بود. فلزات بالاتر در لیست نسبت به فلزات پایینتر آندی هستند به این معنی که وقتی این دو به هم متصل می شوند، فلز بالاتر از فلز پایین تر محافظت میکند و زودتر خورده میشود. در واقع، این حفاظت کاتدی تضمین میکند که حتی اگر پوشش گالوانیزه تا جایی که فولاد (قطر تا 6 میلیمتر) آسیب دیده باشد، هیچ خوردگی شروع نمیشود تا زمانی که تمام فلز روی اطراف مصرف شود.
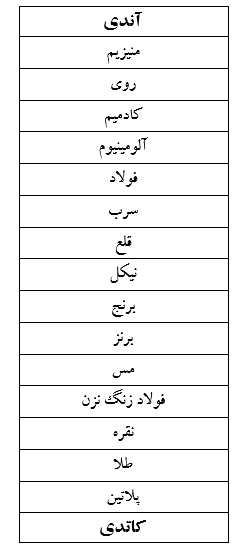
در یک سلول گالوانیکی (شکل 2)، چهار عنصر لازم برای وقوع خوردگی وجود دارد که عبارتند از (1) آند که الکترودی است که در آن واکنش(های) آندی، الکترون تولید میکنند و ماده خورده می شود، (ب) کاتد که الکترودی است که الکترون ها را دریافت میکند و از خوردگی در برابر الکترولیت محافظت میشود، (3) الکترولیت که رسانا است و جریان یونی از طریق آن منتقل می شود و شامل محلول های آبی اسیدها، بازها و نمک ها میشود (پل نمکی در شکل) و (4) مسیر جریان برگشتی که مسیر فلزی اتصال آند به کاتد به یکدیگر است و اغلب همان فلز است (سیم در شکل). هر چهار عنصر آند، کاتد، الکترولیت و مسیر جریان برگشتی برای وقوع خوردگی ضروری هستند. حذف هر یک از این عناصر باعث توقف جریان می شود و خوردگی رخ نمیدهد. جایگزینی یک فلز متفاوت به جای آند یا کاتد میتواند باعث معکوس شدن جهت جریان شود و در نتیجه تغییری در الکترودهایی که دچار خوردگی میشوند، شود. در فولاد گالوانیزه، فلز روی به عنوان آند و فولاد به عنوان کاتد عمل میکند.
فاکتور نهایی در فولاد گالوانیزه برای محافظت طولانی مدت در برابر خوردگی، توسعه زنگار فلز روی است. زنگار فلز روی تشکیل محصولات جانبی خوردگی فلز روی بر روی سطح فولاد است. فلز روی، مانند تمام فلزات، زمانی که در معرض هوا قرار میگیرد شروع به خوردگی میکند. از آنجایی که پوششهای گالوانیزه هم در معرض رطوبت و هم در معرض هوای جریان آزاد قرار میگیرند، محصولات فرعی خوردگی به طور طبیعی روی سطح پوشش تشکیل میشوند. تشکیل این محصولات جانبی (اکسید روی، هیدروکسید روی و کربنات روی) در طول چرخههای طبیعی مرطوب و خشک در محیط رخ میدهد. زنگار روی، پس از تشکیل، سرعت خوردگی روی را تا حدود 30 برابر میزان فولاد در همان محیط کاهش میدهد و به عنوان یک مانع غیرقابل نفوذ برای پوشش گالوانیزه گرم عمل میکند.
فرآیند گالوانیزه کردن
فرآیند گالوانیزه کردن (شکل 3) شامل سه مرحله اساسی است: (1) آماده سازی سطح، (2) گالوانیزاسیون یا گالوانیزه کردن، و (3) بازرسی.
آماده سازی سطح
آماده سازی سطح مهمترین مرحله در اعمال هر پوششی به خصوص تولید فولاد گالوانیزه است. در اغلب موارد، آماده سازی نادرست یا ناکافی سطح علت خرابی پوشش قبل از رسیدن به زمان مورد انتظار است. مرحله آماده سازی سطح در فرآیند گالوانیزه به این علت از اهمیت بالایی برخوردار است که فلز روی به سادگی با سطح فولادی که کاملاً تمیز نیست واکنش متالورژیکی نمیدهد. هر گونه شکست یا نارسایی در آماده سازی سطح بلافاصله بعد از خارج شدن فولاد از فلز روی مذاب آشکار میشود زیرا مناطق نامناسب از نظر تمیزی بدون پوشش باقی میمانند و در این زمان اقدامات اصلاحی فوری لازم است.
آماده سازی سطح برای تولید فولاد گالوانیزه معمولاً شامل سه مرحله است: (1) چربیگیری (caustic cleaning)، (2) اسیدشویی (pickling) و (3) فلاکس زنی (fluxing). در مرحله چربیگیری، یک محلول قلیایی داغ به طور کلی برای حذف آلایندههای آلی مانند خاک، گریس و روغن از سطح فلز استفاده میشود (قلیاشویی). اپوکسیها، وینیلها، قیرها، رنگ و سربارهی جوش همگی باید قبل از گالوانیزه کردن با سنگ زنی، سند بلاست یا سایر وسایل مکانیکی حذف شوند. در مرحله اسیدشویی، پوستهی اکسیدی و زنگ معمولاً با قرار گرفتن در محلول رقیق اسید سولفوریک (H2SO4) داغ یا در اسید هیدروکلریک (HCl) در دمای محیط از سطح فولاد پاک میشوند. آمادهسازی سطحی همچنین میتواند با استفاده از یک مادهی ساینده به عنوان جایگزین یا همراه با تمیز کردن شیمیایی انجام شود. تمیز کردن با استفاده از یک ساینده فرآیندی است که در آن گلوله یا سنگ ریزه فلزی توسط فشار هوا یا چرخهایی که به سرعت در حال چرخش هستند به سمت مواد فولادی پرتاب میشوند.
مرحله سوم، فلاکس زنی است که مرحله نهایی آماده سازی سطح در فرآیند تولید فولاد گالوانیزه است. فلاکس زنی اکسیدها را حذف میکند و از تشکیل اکسیدهای بیشتر روی سطح فلز قبل از انجام عملیات گالوانیزه کردن جلوگیری میکند. روش اعمال فلاکس بستگی به این دارد که آیا در طول عملیات گالوانیزه از فرآیند گالوانیزه تر استفاده میشود یا فرآیند گالوانیزهی خشک. در فرآیند گالوانیزهی خشک، فولاد در محلول آبی کلرید آمونیوم روی (zinc ammonium chloride) غوطه ور و فلاکسزنی میشود. سپس فولاد خشک شده و سپس در فلز روی مذاب غوطهور میشود. در فرآیند گالوانیزهی تر، یک لایه از آمونیوم کلرید روی (zinc ammonium chloride) بر روی فلز روی مذاب ریخته میشود. قطعهی فولادی در مسیر خود از طریق عبور از فلاکس و وارد شدن به داخل فلز روی مذاب، فلاکس زنی و گالوانیزه میشود.
گالوانیزه کردن
در این مرحله، مواد به طور کامل در حمامی شامل حداقل 98 درصد فلز روی مذاب خالص (حمام گالوانیزه) غوطهور میشوند. ترکیب شیمیایی حمام گالوانیزه باید دقیقا مطابق با مشخصات مشخص شده توسط استانداردهای بینالمللی باشد. دمای حمام گالوانیزه در حدود 450 درجه سانتیگراد تا 460 درجه سانتیگراد حفظ میشود. قطعات فولادی ساخته شده تا زمانی که به دمای حمام برسند در حمام غوطهور میشوند. سپس فلز روی با عنصر آهنی که بر روی سطح فولاد است واکنش داده و آلیاژ بین فلزی روی-آهن را تشکیل میدهد. سپس قطعات به آرامی از حمام گالوانیزه خارج میشوند و فلز روی اضافی با استفاده از عملیات خشک کردن با هوا، ارتعاش و یا سانتریفیوژ خارج میشود.
واکنشهای متالورژیکی که منجر به تشکیل و ایجاد یک ساختار از لایههای آلیاژ روی-آهن میشود، تا زمانی که این قطعات نزدیک به دمای حمام گالوانیزه باشند، حتی پس از بیرونکشیدن قطعات از داخل حمام گالوانیزه ادامه دارند. محصولات بلافاصله پس از خروج از حمام در آب یا هوای محیط خنک میشوند. از آنجایی که فرآیند گالوانیزه شامل غوطهوری کامل مواد است، یک فرآیند کامل است یعنی تمام سطوح پوشش داده میشوند. فرآیند گالوانیزه کردن، هم ازسطح بیرونی و هم از سطح داخلی قطعات دارای حفره و سوراخ محافظت میکند.
عواملی که بر ضخامت و ظاهر پوشش گالوانیزه تأثیر میگذارند عبارتند از (الف) ترکیب شیمیایی فولاد، (ب) وضعیت سطحی فولاد، (پ) کار سرد فولاد قبل از گالوانیزه کردن، (ت) زمان غوطهوری در حمام گالوانیزه، (ث) سرعت خروج از حمام گالوانیزه و (ج) نرخ خنک کردن فولاد گالوانیزه.
بازرسی
دو ویژگی پوشش گالوانیزهی گرم که پس از گالوانیزه کردن به دقت مورد بررسی قرار میگیرند، ضخامت پوشش و ظاهر پوشش است. برای تعیین ضخامت، یکنواختی، چسبندگی و ظاهر میتوان انواع آزمایشهای فیزیکی و ساده را انجام داد. محصولات بر اساس استانداردهای بین المللی گالوانیزه میشوند. این استانداردها همه چیز را از حداقل ضخامت پوشش مورد نیاز برای دستههای مختلف قطعات گالوانیزه تا ترکیب فلز روی مورد استفاده در این فرآیند را پوشش میدهند.
فرآیند بازرسی قطعات گالوانیزه، ساده و سریع است و به حداقل نیروی کار نیاز دارد. این ویژگی مهمی است زیرا عموما فرآیند بازرسی مورد نیاز برای اطمینان از کیفیت در مورد بسیاری از پوششهای اعمال شده با قلم مو و اسپری نیاز به نیروی کار زیاد دارند و از نیروی کار ماهر گران قیمت استفاده میکنند.
ضخامت پوشش به طور کلی با استفاده از یک ضخامت سنج مغناطیسی آزمایش میشود. حداقل ضخامت پوشش و الزامات نمونه برداری معمولاً در استانداردهای بین المللی موجود است. استانداردها همچنین دستورالعملهایی را برای تعداد نمونههایی که باید بر اساس اندازه کل قطعات، اندازهگیری شوند را ارائه میکنند. دقیقترین و راحتترین نوع ضخامت سنج مورد استفاده در صنعت، ضخامت سنج مغناطیسی الکترونیکی است.
کیفیت فیزیکی پوشش گالوانیزه
کیفیت فیزیکی پوشش گالوانیزه به پیوند متالورژیکی بستگی دارد. گالوانیزه کردن یک پیوند متالورژیکی را تشکیل میدهد که فلز روی و آهن موجود در فولاد زیرلایه را با یکدیگر ترکیب میکند و مانعی را ایجاد میکند که بخشی از خود فلز است. در طول گالوانیزه کردن، فلز روی مذاب با آهن موجود در فولاد واکنش داده و یک سری لایههای آلیاژ فلز روی-آهن را تشکیل میدهند. شکل 4 یک فتومیکروگراف از سطح مقطع پوشش گالوانیزه بر روی فولاد را نشان میدهد که یک ریزساختار پوشش معمولی متشکل از سه لایه آلیاژی و یک لایه فلز روی خالص را نشان میدهد. مقدار چسبندگی پوشش گالوانیزه به میزان 250 کیلوگرم بر سانتی متر مربع بر روی فولاد زیرلایه است. سایر پوششها معمولاً در بهترین حالت چسبندگی، مقدار چسبندگی حدود 20 تا 45 کیلوگرم بر سانتی متر مربع را ارائه میدهند.
همانطور که بحث شد، تشکیل پوشش گالوانیزه بر روی سطح فولاد یک واکنش متالورژیکی است، به این صورت که فلز روی و فولاد ترکیب میشوند تا یک سری لایه های سخت بین فلزی را تشکیل دهند، قبل از اینکه لایه بیرونی که معمولاً 100٪ فلز روی باشد. اولین لایه از لایههای پوشش، آلیاژ فلز روی-آهن بالای سطح فولاد است که به آن لایه گاما گفته میشود و به طور تقریبی شامل 75 درصد فلز روی (Zn) و 25 درصد آهن (Fe) میباشد. لایه بعدی لایهی دلتا است که دارای حدود 90 درصد فلز روی و 10 درصد آهن است. لایه سوم، لایه زتا، دارای حدود 94 درصد فلز روی و 6 درصد آهن است. ترکیب شیمیایی آخرین لایه (لایه اتا) که با خارج شدن قطعات از حمام گالوانیزه تشکیل میشود، شبیه به ترکیب شیمیایی حمام گالوانیزه است، یعنی فلز روی تقریبا خالص. میتوان در میکروگراف مشاهده کرد که لایه های گاما، دلتا و زتا حدود 60 درصد از کل پوشش گالوانیزه را تشکیل میدهند و لایه اتا حدود 40 درصد باقیمانده را تشکیل می دهد.
در شکل 4، در زیر نام هر لایه، سختی مربوط به آن با یک عدد مشخص شده است که عدد هرم الماس (DPN diamond pyramid number-) نامیده میشود. DPN یک معیار از سختی است و هرچه این عدد بیشتر باشد، سختی نیز بیشتر است. به طور معمول، لایه های گاما، دلتا و زتا سخت تر از فولاد زیرلایه هستند. سختی این لایه ها محافظت بینظیری در برابر آسیب به پوشش از طریق سایش ایجاد میکند. لایه اتای پوشش گالوانیزه کاملاً انعطاف پذیر است و مقداری مقاومت در برابر ضربه به پوشش میدهد. سختی، شکلپذیری و چسبندگی با هم ترکیب میشوند تا پوشش گالوانیزه یک محافظت بینظیر در برابر آسیبهای ناشی از حملونقل در حین جابجایی و یا در محل کار و همچنین در حین سرویسدهی فراهم کند. چقرمگی پوشش گالوانیزه بسیار مهم است زیرا محفاظت از زیرلایه به یکپارچگی پوشش بستگی دارد. پوشش های گالوانیزه که به درستی اعمال شدهاند نفوذ ناپذیر نیز هستند.
در طی واکنش فولاد با فلز روی مذاب در حمام گالوانیزه، دو عامل تعیین کنندهی ضخامت پوشش گالوانیزه است که عبارتند از ضخامت و ترکیب شیمیایی فولاد زیرلایه. علت این موضوع دو پدیده است: (1) به طور کلی، هرچه پوشش فلز روی ضخیم تر باشد، محافظت در برابر خوردگی طولانی تر است و (2) پوشش های بیش از حد ضخیم میتوانند چسبندگی و اتصال کمتری نسبت به پوشش هایی با ضخامت معمولی داشته باشند.
فولادهای مناسب برای تولید فولاد گالوانیزه
اکثر فولادها را میتوان به طور مناسبی گالوانیزهی گرم کرد. با این حال، عناصر واکنشدهنده در فولاد، مانند سیلیسیم و فسفر میتوانند بر فرآیند گالوانیزهی گرم تأثیر بگذارند. از این رو انتخاب مناسب ترکیب شیمیایی فولاد میتواند کیفیت یکنواختتر پوشش را با توجه به ظاهر، ضخامت و صافی ارائه دهد. سابقه قبلی فولاد (به عنوان مثال نورد گرم یا نورد سرد) نیز میتواند بر واکنش آن با مذاب روی تأثیر بگذارد. در مواردی که زیبایی شناسی مهم است، یا جایی که معیارهای خاصی برای ضخامت پوشش یا صافی سطح وجود دارد، توجه ویژه به انتخاب فولاد قبل از گالوانیزهی گرم مورد نیاز است.
ترکیب شیمیایی فولاد، به ویژه مقادیر سیلیسیم، فسفر، منگنز و کربن، بر ویژگیهای پوشش تأثیر دارد. سیلیسیم به طور خاص میتواند تأثیر عمیقی بر رشد پوششهای گالوانیزه داشته باشد. فسفر و منگنز همچنین واکنش پذیری فولاد را افزایش میدهند و در ترکیب با مقادیر سیلیسیم خاص میتوانند پوشش خاکستری مات ضخیمتری ایجاد کنند. مقدار کربن، گوگرد و منگنز فولاد نیز ممکن است تأثیر جزئی بر ضخامت پوشش گالوانیزه داشته باشد.
مقدار سیلیسیم 0.04٪ یا بالاتر و یا مقدار فسفر 0.05٪ یا بالاتر در فولاد معمولاً باعث ایجاد پوششهای ضخیم میشود. برای پوشش های گالوانیزه با بالاترین کیفیت، سطح سیلیسیم باید کمتر از 0.04٪ باشد. فولادهای خارج از این محدوده که فولادهای فعال در نظر گرفته میشوند نیز میتوانند گالوانیزه شوند و معمولاً پوشش قابل قبولی تولید میکنند. با این حال، اغلب پوشش ضخیم تری را تشکیل میدهند و ظاهر تیره تری نیز دارند. این موضوع درمورد فولادهای کشته شده با سیلیسیم حائز اهمیت است زیرا فولادهای کشته شده با آلومینیوم معمولا مقدار سیلیسیم قابل قبولی دارند. مقدار فسفر نیز در فولادهای نورد سرد حائز اهمیت است.
محدوده ساندلین (Sandelin range)
فولادهایی با مقدار سیلیسیم + فسفر در محدوده 0.03 تا 0.14٪ در اصطلاح، “فولادهای ساندلین” نامیده می شوند. از گالوانیزه کردن این فولادها یا باید اجتناب کرد و یا از انواع خاصی از حمامهای گالوانیزه برای گالوانیزه کردن آنها استفاده کرد. در یک حمام گالوانیزهی معمولی واکنش بین این نوع فولادها و فلز روی بسیار قوی است و پوشش ضخیم و غیریکنواخت ایجاد میشود که اغلب با چسبندگی ضعیف همراه هستند. اگر حمام گالوانیزه با افزودنی های آلیاژی مناسب در دسترس نباشد، از این نوع فولاد برای گالوانیزهی گرم باید اجتناب شود.
مطالعات اخیر درمورد مقدار سیلیسیم و فسفر درمورد فولادهای مختلف به نتایج زیر رسیده اند. اگر ظاهر سطح گالوانیزه بسیار مهم باشد، به عنوان مثال در کاربردهای معماری، مقداری که برای فولاد نورد سرد توصیه میشود عبارت است از سیلیسیم کمتر از 0.03 درصد و سیلیسیم + 2.5 برابر فسفر کمتر از 0.04 درصد. برای فولاد نورد گرم مقدار سیلیسیم مهمتر است و مقدار فسفر از اهمیت کمتری برخوردار است و مقداری که توصیه میشود عبارت است از سیلیسیم کمتر از 0.02 درصد و و سیلیسیم + 2.5 برابر فسفر کمتر از 0.09 درصد. اگر گالوانیزه کردن در یک حمام حاوی نیکل انجام شود، که امروزه رایج است، واکنش پذیری بیشتر کاهش مییابد و در نتیجه لایه های پوشش نازک تر می شوند.
فولاد کشته شده با آلومینیوم
فولادهای کشته شده با آلومینیوم نیز حاوی مقدار کمی سیلیسیم هستند. در سالهای اخیر که فولاد کشتهشده با آلومینیوم رایجتر شده است، مقدار سیلیسیم کم در ترکیب با مقدار بالای آلومینیوم، لایههای فلز روی را نازکتر از آنچه در استانداردها بیان شده است، میسازد.
ظاهر پوشش
گالوانیزهی گرم فولادهای با مقدار سیلیسیم یا فسفر کم، باعث تشکیل پوششهای روشن و براق میشود. در محیط های بیرونی، رنگ سطح پس از مدتی به رنگ مات و خاکستری روشن تغییر میکند. فولادهایی با مقدار سیلیسیم در محدوده 0.15 تا حدود 0.23٪ معمولاً پوشش های روشن و براق میدهند. مقدار سیلیسیم در حدود 0.25٪ می تواند سطوح خاکستری یا شبکه خاکستری را روی یک سطح روشن ایجاد کند. اگر از حمام فلز روی حاوی نیکل استفاده شود، واکنش بین فلز روی و آهن کاهش مییابد و پوشش معمولاً تا 0.22 درصد سیلیسیم، به رنگ روشن است.
فولاد با مقدار سیلیسیم بالاتر (بیشتر از 0.25٪) معمولاً پوشش های مات و خاکستری ایجاد میکند که با افزایش مقدار سیلیسیم تیرهتر میشود. رنگ خاکستری تیره فقط یک اثر زیبایی شناختی است، زیرا تا زمانی که ضخامت پوشش یکسان باشد، محافظت در برابر خوردگی یکسان یا حتی بهتر است. پوششهای خاکستری تیره اغلب ضخیمتر از پوششهای روشن هستند، زیرا معمولاً به دلیل واکنشپذیری بالاتر بین آهن و فلز روی ضخیمتر هستند و از این رو محافظت در برابر خوردگی طولانیتری دارند. رنگ پوشش با نسبت کریستال آهن-روی به فلز روی خالص در سطح بیرونی پوشش تعیین می شود. هنگامی که یک پوشش فلز روی با محتوای آهن بالا دچار خوردگی میشود، آهن اکسید میشود، که میتواند رنگی قرمز مایل به قهوه ای به سطح بدهد، بنابراین تغییر رنگ سطح به قرمز مایل به قهوهای به این معنی نیست که پوشش از بین رفته است.
فرآیند گالوانیزه مداوم
فرآیند پوشش دهی گرم پیوسته روشی پرکاربرد است که در ابتدا در دهه 1960 میلادی برای تولید فولاد گالوانیزه بصورت ورق، نوار و سیم توسعه یافت. پوشش مذاب در یک فرآیند مداوم بر روی سطح فولاد اعمال می شود. فولاد به عنوان یک نوار پیوسته از داخل حمام فلز روی مذاب با سرعت تا 200 متر بر دقیقه عبور داده میشود. اندازه ورق فولادی می تواند از 0.25 میلی متر تا 4.30 میلی متر ضخامت و تا 1830 میلی متر عرض باشد.
فرآیند گالوانیزهی مداوم با تمیز کردن فولاد در یک واحد که معمولاً از یک مایع قلیایی همراه با برس زنی، شستشو و خشک کردن استفاده میکند، آغاز میشود. سپس فولاد به داخل کوره پیش گرم می رود تا نرم شود و استحکام و شکل پذیری مورد نظر ایجاد شود. دمای کوره در این مرحله معمولا بین 730 تا 780 درجه سانتی گراد است. در این کوره، فولاد تحت یک اتمسفر گاز احیا کننده متشکل از هیدروژن و نیتروژن نگهداری میشود تا هرگونه اکسیدی که میتواند روی سطح فولاد باشد حذف شود. انتهای خروجی کوره با یک محفظه خلاء به حمام پوششدهی مذاب متصل میشود تا از اکسید شدن مجدد محصول فولادی گرم شده توسط هوا جلوگیری شود. در حمام گالوانیزه، محصول فولادی با فلز روی مذاب واکنش میدهد تا پوشش پیوندی ایجاد کند و سپس در جهت عمودی خارج میشود. هنگامی که محصول از حمام خارج میشود، هوا با فشار بالا برای حذف فلز روی مذاب اضافی برای ایجاد ضخامت پوشش کاملاً کنترل شده استفاده می شود. سپس فولاد خنک میشود تا فلز روی سطح فولاد منجمد شود، این کار قبل از تماس فولاد با رول دیگری انجام میشود تا از انتقال یا آسیب رساندن به پوشش جلوگیری شود. شکل 5 بطور شماتیک مراحل انجام فرآیند گالوانیزه مداوم را نشان میدهد.
کاربرد ورق گالوانیزه
ورق فولاد گالوانیزه به دو بخش ورق آهنی گالوانیزه و ورق فولاد گالوانیزه تقسیم بندی می شوند. در ورق آهنی گالوانیزه، آهن توسط عنصر روی پوشش داده شده و در ورق فولاد گالوانیزه، ورق فولاد با عنصر روی پوشانده می شود. از این ورق های گالوانیزه در پنل ها و تابلو برق ها، مجراهای هوا و دودکشها، ناودانی ها و در لوله، بدنه و سقف سوله ها، لوله بخاری، کانال های کولر، کابینت مورد استفاده در آشپزخانه، سقف شیروانی خانه ها در مناطق مرطوب از آهن گالوانیزه استفاده می شود.
از ورق گالوانیزه نیز در صنایع خودرو سازی استفاده می شود. به غیر از بدنه خودرو، بسیاری از قطعات خودرو همچون شاسی ماشین ، چرخ ، ترمز ها، ستون خودرو، سیستم اگزوز و در موتور نیز از ورق فولاد گالوانیزه می باشد.